The debate about Differences Between laser cutter vs. Waterjet wood cuttier can be better understood only after a cursory evaluation.
For starters, laser and waterjet cutting are both processes used in industrial manufacturing.
Even though laser cutting and water Jet cutting are both used industrially for the same purpose, they still have some clear differences.
The functionality of each method makes it more suitable for a particular project depending on the industry requirements.
When a laser Cutter or Waterjet connects to a computer, they become CNC (computer numerical control) milling machines.
CNC machines only require a programmed pattern to carve the shapes and lines required.
It does not require the active involvement of a human to drill or cut shapes into materials.
When choosing a fabrication cutting tool for your factory, it is important to note the needs you hope to meet.
This will help you choose the option that is more apt to meet your factory’s needs.
This blog post discusses the differences and similarities between Waterjet and laser-cutting machines.
The purchase will serve as a guide for choosing the best fabrication-cutting machine for your factory.
Waterjet Cutting – How it works
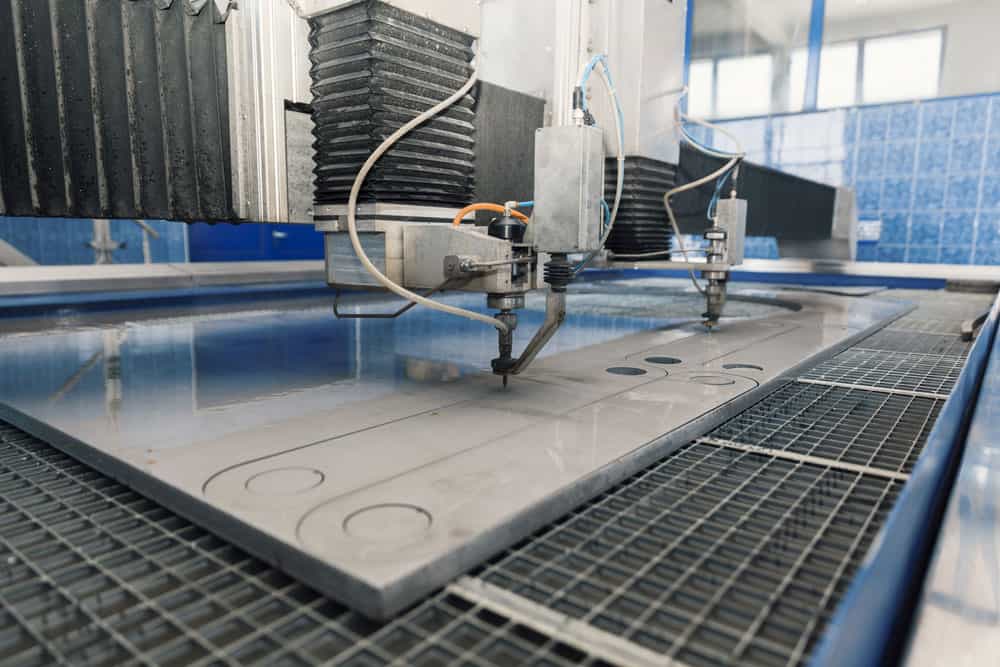
A Water jet cutter
Waterjet cutting involves cutting materials by utilizing a technique called accelerated erosion. Waterjet cutters work with abrasives such as garnet sand to increase the force of the water hitting the material.
Highly pressurized water rushes through a ceramic or diamond nozzle into a mixing chamber.
The water pressure creates a vacuum and draws garnet sand into the stream, where it then hits the targeted object, causing a high-speed fluvial erosion on the material’s surface.
Waterjet uses a pressure of as high as 60000 pounds per sq. inches (4137 bar) in cutting materials.
The use of abrasives in waterjet cutting makes it possible to cut through very thick objects.
Waterjets have no limit to the materials they can cut through-woods, metals, stone, etc.
They can make cuts as deep as 10 – 12 inches in hard materials at high speed.
The thickness of the material determines how fast a Waterjet can cut through a material.
The Pros of Waterjet
- Waterjet cutting has no limitations to the materials it can cut through. This is one property that gives this method an advantage in every industry. Whether you work on wood, ceramics, glass, thick metal, wood, etc., water Jets can be an appropriate CNC machine for cutting and shaping patterns.
- Water jet cutters cut through very thick materials. Given the necessary time, a water jet can cut through materials of any depth.
- It does not consume a lot of water. Even though water is its major component, it does not consume as much water as you might fear it to consume.
- It has very good cutting precision. Waterjets have good precision, especially when used as a CNC machine.
- No heat affected zone. Because water jets do not generate much heat, they become more appropriate for heat-sensitive materials. Materials such as plastic, acrylics, composites, etc., are better worked on using Waterjet cutting.
Cons of Waterjet
- Leaves a lot of waste. Waterjets require a bit of cleanup because of the abrasives mixed in the water.
- Thin, small materials require extreme carefulness because of the high force applied.
Laser Cutting – How it Works
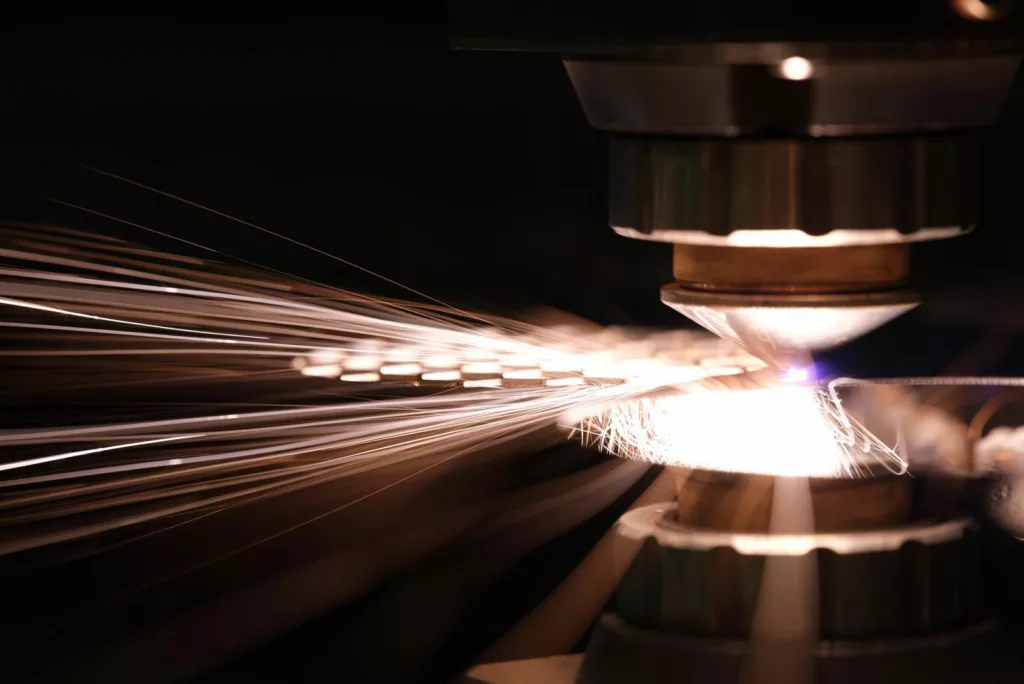
The Laser cutting of metal sheets, close laser optics, and CNC
Laser cutting employs heat in separating materials. A laser beam as thin as a hair strand hits a particular target material surface.
It heats it so strongly that it melts or completely vaporizes. The cutting process is also aided by compressed gasses.
In addition to cutting, laser cutters are also used for engraving patterns into materials. This feature gives it an advantage over Waterjet.
This comes in handy when serial numbers, markings, or aesthetic designs are needed.
Laser cutters are very precise in cutting thin materials. They can make clean cuts through a material a little above one inch thick.
However, their optimal performance comes in cutting metals that are about ½ inch thick or less.
Pros of Laser cutters
- Very precise cutting on thin metals. Lasers are very precise in cutting and shaping thin materials. It does not apply pressure on the material hence reducing the risk of breaking or distortion due to pressure.
- It can cut through a variety of metals and nonmetals, including wood.
- Appropriate for creating complex patterns. Laser is more suitable for cutting complex patterns on materials as a CNC machine.
Cons of Laser Cutting
- Not appropriate for thick materials. Laser cutting can only give accurate cut-through materials of about 1 inch thick.
- It cannot be used for heat-sensitive materials. Heat can alter the properties of some materials. Laser-cutting machines are not suitable for such materials, for example – marble.
Waterjet Vs. Laser Cutting; their similarities and Differences

A Waterjet cutting machine
Comparing the two methods will make it easier for you to understand the best fit for your factory. The measures considered below are only used as a factor for comparison.
Rating one method below the other does not necessarily make it inferior to its counterpart. There can only be one most suitable method for every necessity.
Range of material
Waterjet stands out at this level, considering that it has no limitations in materials it can cut through.
Laser Cutter, on the other hand, is more limited in the materials it can work on.
Thickness
Waterjet cutting has no competition when it comes to cutting very thick materials. Laser cutters are more suitable for cutting thin materials.
Safety
Laser cutters are safer to handle. However, they are both harmful when mishandled and can cause serious disfigurement if accidentally touched the body.
Costs
The cost of purchasing a laser cutting machine is a little above that of Waterjet.
However, in terms of tooling and component costs, laser-cutting machines are cheaper, considering that there is no tooling.
The laser tube itself can last an average of two years.
A Waterjet is costlier due to component wear and consumables. In addition to the periodic maintenance of the water pump, the machine requires nozzles, seals, water, and an abrasive medium for steady running.
Quality and precision
Laser cutting is the best method when precision and quality are important factors.
Laser cutting can give accuracy up to +/0.005. Waterjet has a fairly high precision accuracy of up to +/0.02.
Cutting speed
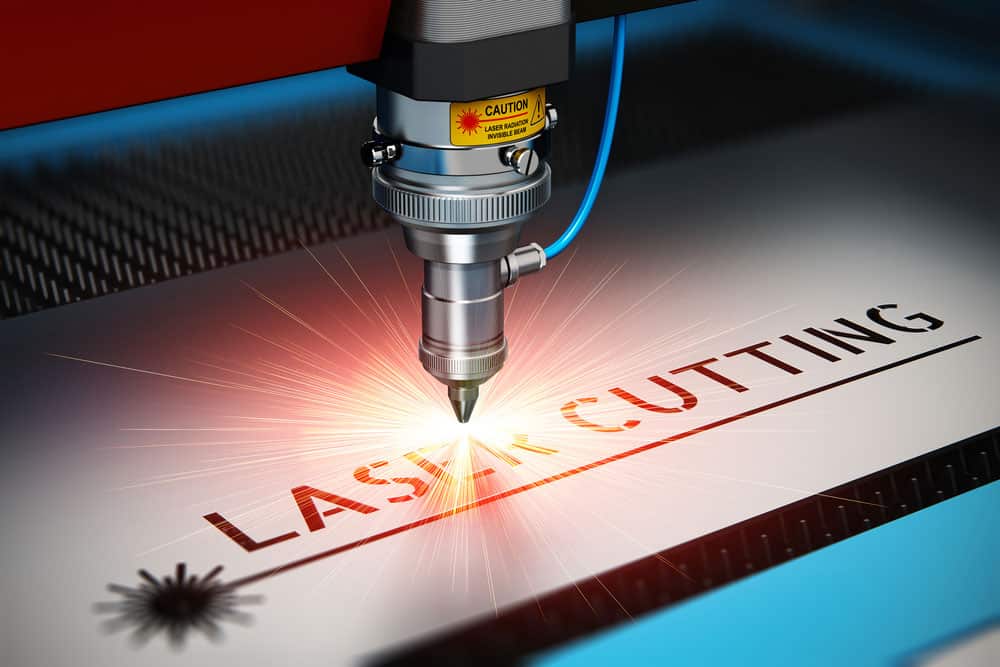
the Laser cutting technology
Laser Cutter is about 3 times faster than Waterjet. Laser cutters are most often employed when handling a large industrial project.
They are more suitable for the massive production of shapes and patterns.
Maintenance
Water jets require steady maintenance. The water pump needs frequent maintenance.
There is also a need to change tools like nozzles, seals, and abrasives. On the other hand, laser cutters require less maintenance and tooling.
Safety, Noise, and Waste Concerns
Laser cutting involves very low risk. It does not require safety goggles, but one can never be too careful when handling an industrial machine.
Proper ventilation is also important when working with a laser cutter because of the dust and smoke generated. The dust and smoke can be slightly toxic.
On the contrary, water jet cutting involves more risk. Safety wears, such as gears, covers, and safety glasses, is necessary for protection against pressured water.
Laser cutting is quiet and easy, unlike Water jets which generate a lot of noise and nuisance.
The noise pollution from water jets can be so extreme that you must wear ear protection.
Water jet cutting requires more cleanup after use. This results from the abrasives mixed with water and large quantities of cutting wastes left behind.
Laser cutting, on the other hand, requires less cleanup. This method only generates a small amount of dust and smoke.
Common Uses
The water jet and laser cutting are industrial methods employed in cutting and shaping various materials to meet industrial needs.
Conclusion
In summary, laser cutting gives a very high precision when working on a more detailed pattern. It is also suitable for engraving.
On the other hand, Waterjet cutting has no material limitation and can cut through very thick sheets.